摘 要:研究了在熱等靜壓低壓工藝參數下,T15 粉末高速鋼組織中析出粗大碳化物的現象,粗大碳化物使材料性能大大降低,并且發現很難通過后續的鍛造和熱處理手段加以消除,因而提出:合理選擇粉末高速鋼致密化工藝參數是十分必要的。
關鍵詞:粉末高速鋼;熱等靜壓;壓力;碳化物
中圖分類號:TF12 文獻標識碼:A 文章編號:1672- 545X(2010)01- 0006- 03
粉末高速鋼優于熔煉高速鋼最主要的特點,就是在合理的燒結工藝下能夠幾乎完全抑止粉末內部的合金元素偏析和粗大碳化物析出,使得碳化物均勻細小彌散分布在組織中,大
大提高了力學性能和使用性能
[1~2]。粉末高速鋼的致密化工藝多種多樣,如熱等靜壓工藝、噴射成型工藝、擠壓成型工藝等,但是最常采用的路線還是霧化制粉 + 熱等靜壓(HIP)。在合理的熱等靜壓工藝參數下,粉末高速鋼結構致密,碳化物顆粒非常細小,且呈彌散分布。國內外很多學者研究了熱等靜壓工藝參數,包括溫度、時間和壓力對碳化物尺寸、 形貌、種類及其機械性能的影響。本文主要研究在熱等靜壓低壓工藝參數下,
T15 粉末高速鋼組織中析出大尺寸碳化物,使材料性能大大降低,并且發現,很難通過后續的鍛造和熱處理手段消除粗大碳化物。
- 實驗材料與步驟
本文實驗研究的原料為 T15 高速鋼粉末。粉末經過篩分、裝套、抽氣、封焊后,在熱等靜壓機(型號為 QIH- 15 型熱等靜壓試驗機) 中燒結,后經過精鍛和熱處理。利用 LEO- 1450
(British)型帶有背散射和能譜分析儀(EDS)的掃描電子顯微鏡(SEM)和光學顯微鏡分析粉末形貌、鋼坯的組織、碳化物的種類及其斷口形貌。
- 結果分析
2.1 粉末形貌
T15 粉末高速鋼成分如表 1 所示,可知粉末合格,氧含量達標。我們所用的粉末通過了 200 目的篩子,粉末形貌如圖 1所示,
圖 1(a)為二次電子照片,圖 1(b)為背散射電子照片,從背散射電子照片中,可以看到粉末顆粒中的碳化物非常細小。
|
表 1 |
T15 粉末化學元素含量表 |
(%) |
|
|
|
|
|
|
|
C |
P |
S |
Cr |
Mo |
V |
W |
O |
|
|
|
|
|
|
|
|
1.62 |
0.025 |
0.001 7 |
4.20 |
0.11 |
4.81 |
12.00 |
0.012 |
|
|
|
|
|
|
|
|
Co |
Mg |
Ca |
Al |
Si |
N |
H |
|
|
|
|
|
|
|
|
|
4.79 |
0.000 5 |
0.000 5 |
0.021 |
0.16 |
0.11 |
0.000 5 |
|
- 熱等靜壓低下形成的組織
所選熱等靜壓壓力為 65 MPa,溫度為 1 150 ℃,保溫 3 h,壓坯組織圖如 2(a)所示,得到了粗大碳化物,最大尺寸可達15~20 μm,并且粗大的碳化物大多數都在三個顆粒的邊界交叉處聚集長大,經過熱處理后,硬度最高只能達到 65 HRC,抗彎強度最高只有 2 000 MPa 左右,還不及熔煉高速鋼的水平。斷口組織如圖 3 所示,可看到斷裂基本上是沿著大尺寸碳化物組織發生。碳化物主要是碳化鎢和碳化釩,析出的大尺寸碳化物是性能較低的主要因素。在 65 MPa 的壓力下,把熱等靜壓溫度降低了 50 ℃,壓坯組織圖如 2(b)所示,碳化物尺寸沒有減小,與圖 2(a) 組織圖沒有多大差別,因此我們排除了溫度這個影響因素。并且粉末中的碳化物也是細小彌散分布的,可知大尺寸的碳化物形成主要是我們采用了低壓,一般壓力應該在 100 MPa 以上
[3~4]。
- 粉末高速鋼中碳化物粗化機理為了分析的需要,本文將 T15 粉末高速鋼析出的碳化物進行了分類,碳化物根據在鋼中析出的位置,可分為兩大類:第一類是在顆粒內部析出,第二類是在顆粒之間析出。

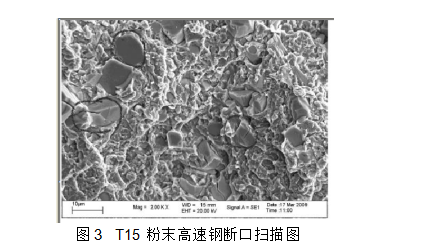
對第一類碳化物的形成機理,提出如圖 4 所示的碳化物形成過程
[3]。其主要過程是液相與固相共存區,降低溫度冷卻時,液相首先轉變為奧氏體相(即 L → γ),隨后溫度繼續降低,在奧氏體相之間剩余的液相發生共晶轉變,轉變為奧氏體和碳化物(即 Le → γ + 碳化物),直到最終全部轉變為固相為止,此類碳化物在顆粒內部,抑制了碳化物的長大。對于第二類碳化物,結合熱等靜壓的原理以及碳化物析出的形貌分析,本文提出了碳化物析出-聚集長大的碳化物粗化模型(如圖 5 所示),在高壓條件下,顆粒間比較致密,顆粒間形成的碳化物比較細小;在低壓條件下,顆粒間比較疏松,顆粒間形成的碳化物就比較粗大。
為了進一步解釋本文提出的碳化物析出-聚集長大的碳化物粗化的模型,從熱力學和動力學方面進行了分析。圖 6 為高速鋼偽相圖,T15 粉末高速鋼含碳量為 1.5% ~ 1.6%,在1 100~1 150 ℃的熱等靜壓溫度下,組織中存在液相、碳化物和奧氏體化區域,也就是說在保溫加壓階段,碳化物已經開始析出。因為顆粒大多數為球形,所以當壓力過低時,在顆粒與顆粒之間會存在較大的空隙,由于顆粒邊界能量較高,碳化物優先在顆粒邊界析出,這時候顆粒邊界析出的碳化物,會輕而易舉的占據這個空隙,與相近的碳化物接觸,從而聚集長大,形成了粗大的碳化物。這時候的熱等靜壓壓坯的致密,其實是偽致密,甚至有時候會出現所測密度大于理論密度的現象。而當壓力提高時,顆粒受到較大壓力的作用,形狀發生改變,朝著有利于顆粒之間空隙減小的方向發展,結果就是顆粒之間的空隙大大減小甚至消失。這時候在顆粒間隙上形成的碳化物尺寸,也就相應大大的縮小,碳化物會細小均勻地彌散在顆粒中,這和圖 2 所示的實驗結果是一致的。
- 7 為吳引江等人研究的在不同壓力下,在 900 ℃ 保溫3 h 熱等靜壓機中,Ti- 5Al- 2.5Sn 粉末顆粒界面的形態,圖 7(a)中顆粒形狀基本沒有太大變化,仍為初始的圓形,并且顆粒之間有很大的間隙,當壓力增大時,顆粒變形較大,顆粒間的空隙消失,這也證實了我們的模型圖。
- 熱處理和鍛造工藝對大尺寸碳化物的影響析出的大尺寸碳化物,是阻礙性能提高的主要因素。我們隨后對這種低壓下制備的 T15 鋼進行了鍛造和熱處理,希望能通過鍛造和熱處理減小碳化物的尺寸。
(1)鍛造。眾所周知,鍛造可以細化晶粒。圖 8(a)為鍛造比為 3:1 時鍛造后的組織,與熱等靜壓壓坯組織相比,碳化物尺寸幾乎沒有減小,于是我們加大鍛造比改為 5:1,有局部地方出現了鍛裂的情況,但是組織中的碳化物尺寸還有沒有多大變化,如圖 8(b)所示。因此,通過鍛造手段對于在粉末冶金致密化過程中形成的碳化物尺寸的減小,幾乎不起作用。
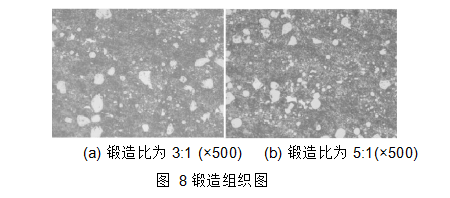
(2)熱處理。正確的熱處理工藝,對于提高粉末高速鋼的性能是非常必要的,T15 粉末高速鋼的淬火溫度大概為1 230~1 260 ℃,我們選擇了 1 240 ℃,希望通過延長淬火保溫時間來溶解大尺寸的碳化物。我們取了直徑為 10 mm 的小樣,分別保溫 0.5 h、1 h 和 1.5 h 作為對比,圖 9 為淬火后的組織圖。由圖 9(a)可以看到,保溫 0.5 h 晶粒未長大,但是碳化物尺寸并沒有減小;由圖 9(b) 可以看到,保溫 1 h 后晶粒明顯長大,但是碳化物尺寸沒有改變;而圖 9(c) 保溫 1.5 h 后,晶粒明顯長大,并且伴隨著少量的晶界熔化,而碳化物尺寸仍然沒有減小的趨勢。由此我們可以知道,延長熱處理保溫時間對減小碳化物的尺寸,也是沒有效果的。由于大尺寸的碳化物主要分布在顆粒邊界處,顆粒邊界由于氧化物等雜質元素富集,這些都增加了碳化物溶解的阻力。